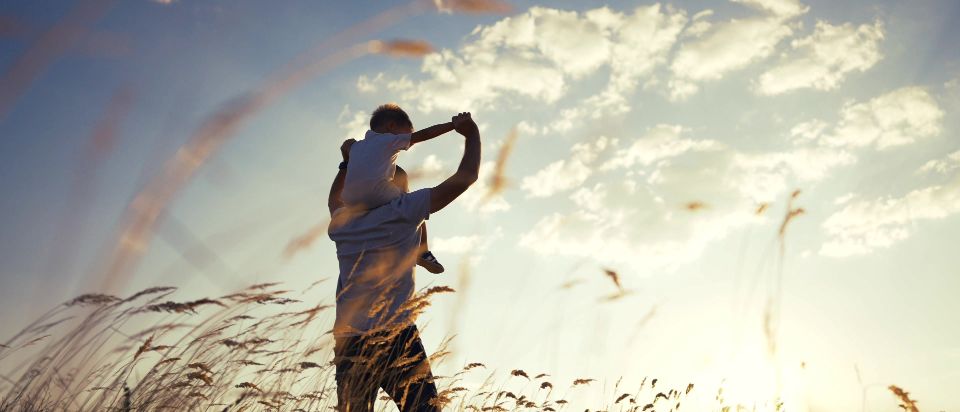.jpg)
Sustainability
Reduce our CO2 impact for generations to come
In today’s world, having accurate and transparent data is essential for businesses striving to reduce their environmental impact. At Trespa, we’re committed to making that clear and factual for you. The TRESPA STANDARD is a fact-based approach, it’s a promise of transparency and accountability that you can rely on.
Our panels are designed to reduce CO2 emissions, they do store CO2 throughout their lifetime, and we provide the detailed information on CO2 footprint you need to ensure your project meets and exceeds sustainability targets.
OUR FOCUS IS REDUCING CO2 EMISSIONS
Wood based product
Our panels are made using up to 70% wood fibres, which capture and store carbon, contributing to CO2 reduction. Wood is a sustainable, natural and renewable resource.
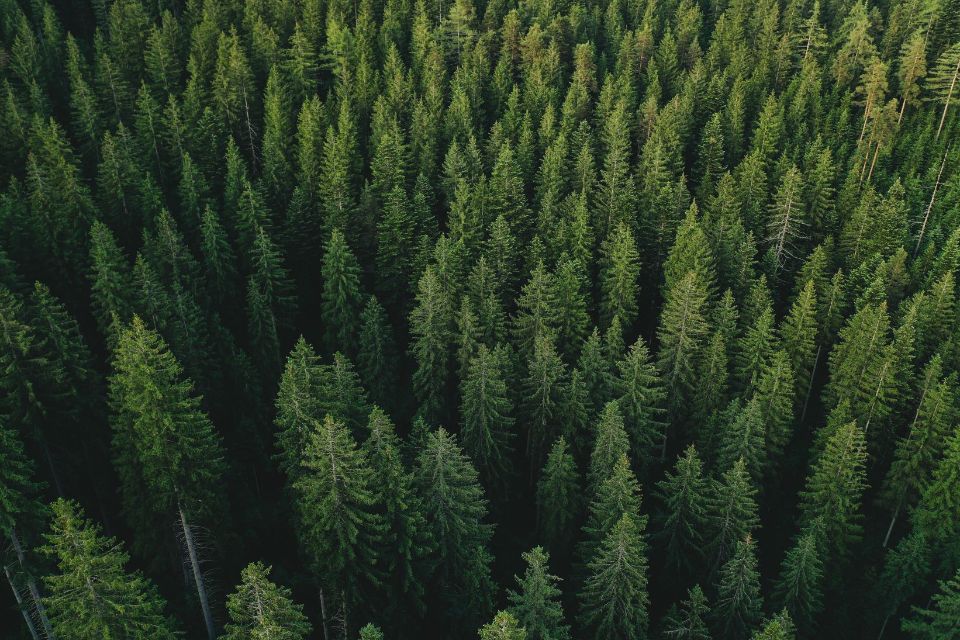
Energy-efficient production
We continuously optimise our production processes to reduce energy consumption and emissions, making sustainability part of our manufacturing DNA. We are proud to power our operations with 100% green electricity.
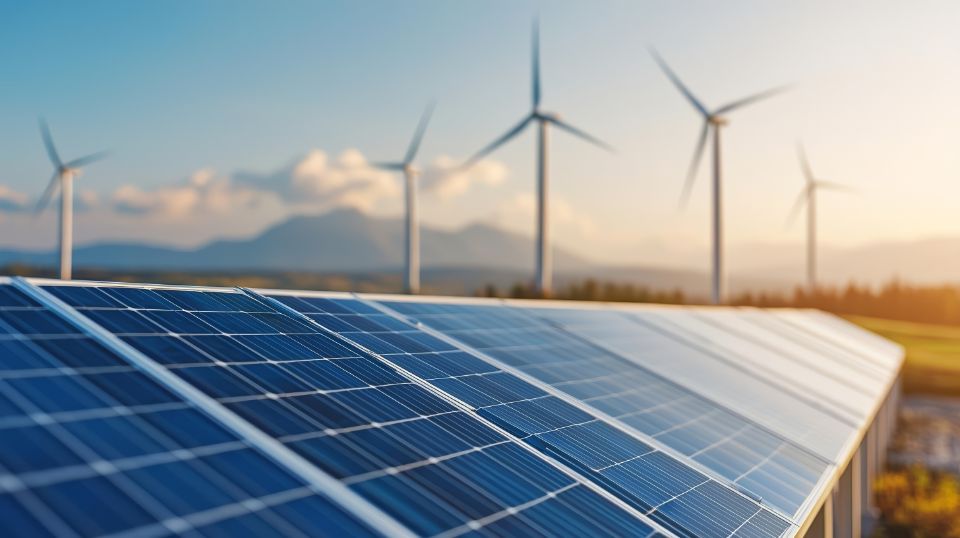
Extended lifespan panel
With an extreme durability, Trespa panels retain stored carbon for longer periods. With our Second Life Program, we further extend the use of panels, cutting CO2 emissions and reducing waste.
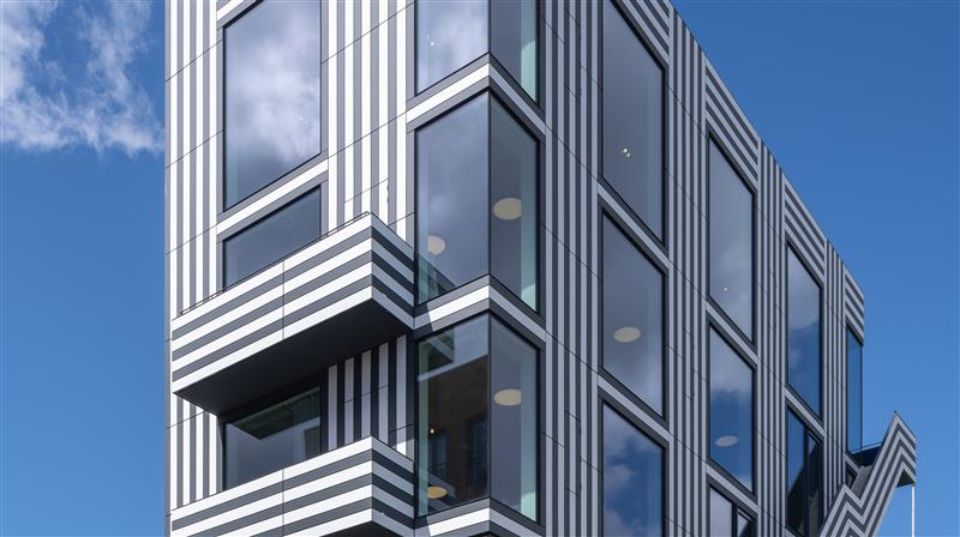
Data-driven accountability
Every sustainability claim we make is backed by data. We believe in measurable impact, holding ourselves accountable with transparent, third party verifications.
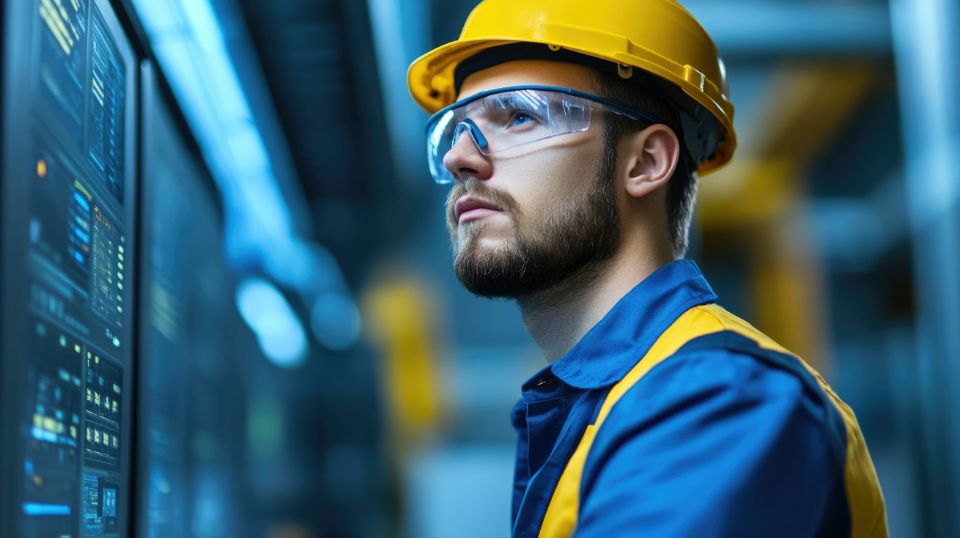
TRESPA STANDARD ON SUSTAINABILITY
Using up to 70% wood fibres, they capture and lock in CO2 absorbed by trees during their growth. When used in ventilated facades, these panels improve energy efficiency by cutting emissions from heating and cooling, helping reduce your project s overall carbon footprint. With our reuse program Trespa Second Life, our used panels find new purpose beyond facades reimagined as chairs, sheds, and more. This extends their carbon-storing ability, offering a sustainable solution that goes beyond building performance to reduce emissions over the long term.
Trespa panels are low carbon products for sustainable buildings
Trespa® Meteon® carbon footprint (std grade) : 3,75kg CO2 eq./m². Environmental Product Declaration A1-A3 (production stage) for 8mm product thickness
Trespa® Toplab® PLUS ALIGN carbon footprint : -7,64kg CO2 eq./m². Environmental Product Declaration A1-A3 (production stage) for 16mm product thickness
Our focus is CO2 carbon emissions explained
TRESPA SECOND LIFE PROGRAM
The Second Life Program is our reuse program, is our commitment to a circular economy. By transforming panels at the end of their initial use into entirely new products, we reduce waste, lower disposal costs, and extend the lifespan of the materials—keeping carbon locked in for longer. Each panel reused through this program cuts CO2 emissions by up to 25% over the product’s lifespan, making it a significant step toward a more sustainable future.
TRESPA'S JOURNEY TO DO MORE AND BETTER
Here are some of our key achievements so far:
85% bio-based materials
We’ve incorporated up to 85% bio-based content into products like Trespa® Toplab® PLUS ALIGN, reducing dependency on fossil-based raw materials.
100% renewable electricity
Since 2020, all of our manufacturing has been powered by renewable energy, reducing our operational carbon footprint.
Looking forward for carbon neutrality:
We’re not done yet. With each step forward, we continue to set new targets that push the industry toward a more sustainable future.
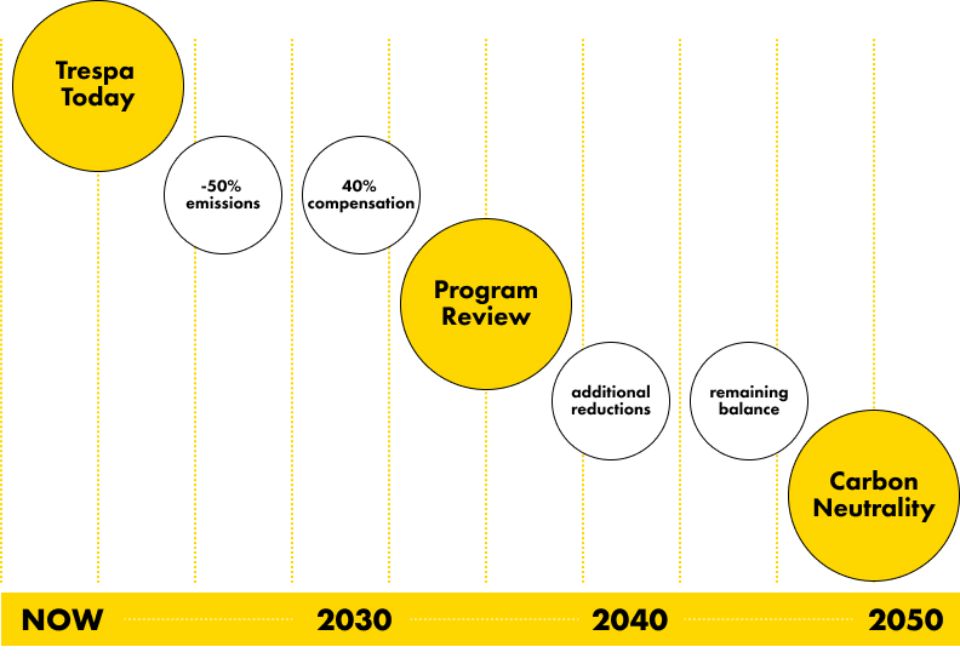
You can find all relevant certifications and documentation here
LET'S CHALLENGE THE STATUS QUO
With The Trespa Standard, we're setting bold new benchmarks in sustainability, transparency, and responsible innovation. Our commitment to clear communication and data-driven solutions empowers you to design smarter, greener projects that make a real impact.
Together, we can change the way we build
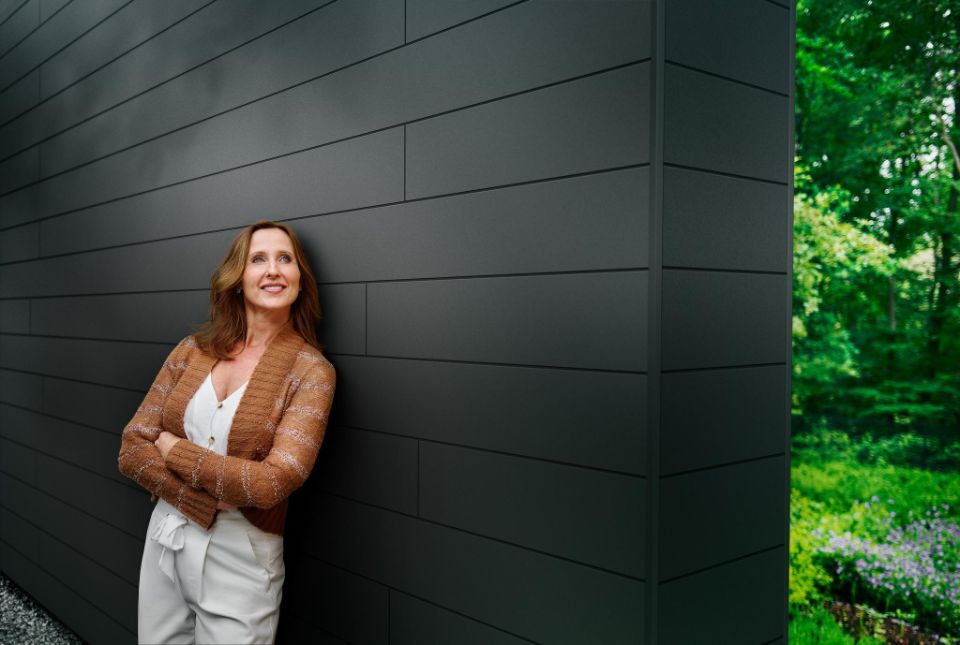.jpg)